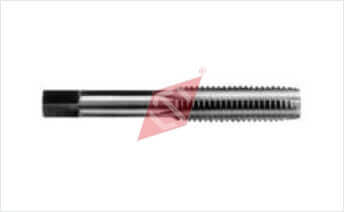
These standard style taps have straight flutes of a number specified as either standard or optional. Hand taps are for general purpose applications such as production tapping or hand tapping operations.
Taper, plug and bottoming styles provide versatility in tough materials, blind and through holes.
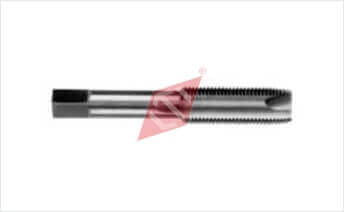
These standard style taps have straight flutes of a number specified as either standard or optional. Hand taps are for general purpose applications such as production tapping or hand tapping operations. Taper, plug and bottoming styles provide versatility in tough materials, blind and through holesAs to general physical dimensions, spiral point taps are identical with the standard hand tap.
However, the spiral point tap has the cutting face of the first few threads cut at a pre-determined angle relative to the tap’s axis angle to force the evacuation of chips ahead of the cutting action. This feature, plus the excellent shearing action of the flute, make spiral pointed taps ideal for production tapping of through holes. Typically, this type of tap has a shallower flute passage than conventional taps. This gives the spiral point tap more cross-sectional area, which means greater strength, allows higher tapping speeds, and requires less power to drive.
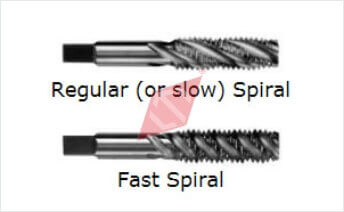
These taps, as the name implies, are made with spiral flutes instead of straight flutes. This spiral fluting feature aids in drawing chips out of a hole, or serves to bridge a gap inside the hole such as a keyway or cross-hole.
Commonly available in slow spiral (25-30¡ helix angle) or fast spiral (45-60¡).
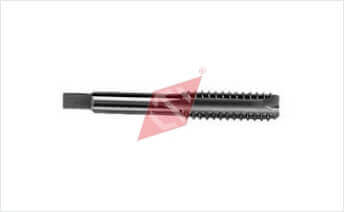
These taps have an odd number of lands with alternate teeth in the thread helix removed. The removal of every other tooth helps to break the chip and allows a greater supply of lubrication to reach the cutting teeth, reducing the incidence of torn threads. Ideal for tapping non ferrous metals and low carbon steel; as well as use in titanium and high hardness alloys.
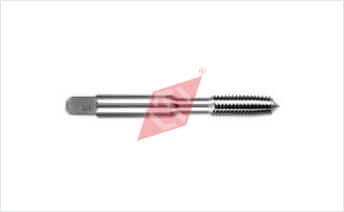
These taps are fluteless except as optionally designed with one or more lubrication grooves. The thread form is lobed so there is a finite number of points contacting the work. This tap does not cut, so it is ‘chipless’, and consequently will not cause a chip problem. The tool forms the thread by extrusion, thus thread size can be closely maintained.
The fluteless design allows high quality threads, faster tapping speeds, higher production, and generates no chips which simplifies tapping of blind bottoming holes (threads can be formed the full depth of the hole).
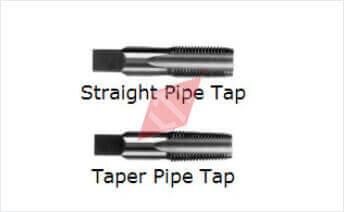
These taps are for producing standard straight or tapered pipe threads in a wide range of pipe connections. Manufactured with the appropriate design variations to cut specified pipe thread forms.
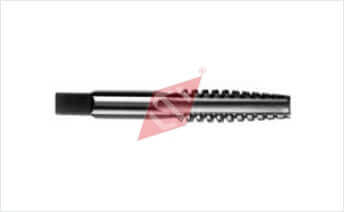
Acme screw threads were devised to allow rotary and transversing motion on machines; and are also used in jacks, valves, presses and other mechanisms where heavy loads are encountered. The acme thread is characterized by a 29° included angle.
Acme taps typically require specialized engineering and design due to the nature and severity of cut required in producing Acme threads.
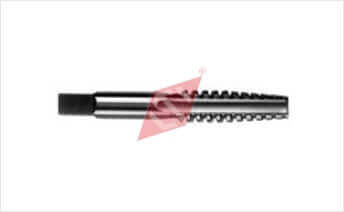
Trapezoidal screw threads were devised to allow rotary and transversing motion on machines; and are also used in jacks, valves, presses and other mechanisms where heavy loads are encountered.
The trapezoidal thread is characterized by a 30° included angle. Trapezoidal taps typically require specialized engineering and design due to the nature and severity of cut required in producing trapezoidal threads.(These are the metric equivalent of Acme Taps but with a 30° included angle).
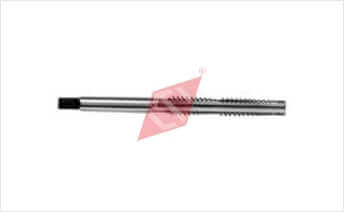
These taps combine the initial roughing cut with the final finishing cut, in one pass, to achieve an acme screw thread. These taps are economical and enhance production levels by saving on the operation of two tools. Since acme thread pitches are generally coarse relative to diameters, these taps are subjected to heavy chip loads.
To achieve a high quality acme thread in a cost-effective manner, roughing and finishing operations are recommended.
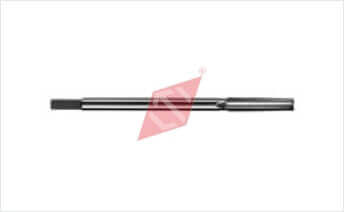
Nut taps feature a long chamfer which assists in entering the drilled hole, and distributes the cutting action over several teeth. These taps were initially designed for tapping nuts and have a long thread length.
The shank diameter is smaller than the tap’s minor diameter to allow the accumulation of several nuts after tapping. Nut taps also feature an extended square length.